Welcome to the future of diesel repair! Technological advancement has completely revolutionized the world of diesel truck repair. Starting from the emergence of AI-enabled diagnostic tools to 3D printing and virtual reality. Mechanics are adjusting accordingly to these tech trends to get more effective and affordable, yet accurate in their repairs.
In this blog, we shall delve into some tech innovations that are defining the future of diesel repair and how your local mechanic is adjusting to these changes to better serve you while keeping your diesel truck on a smooth run.
Rise of AI in Diesel Repair
AI has initiated a revolution in the field of diesel repair. With AI-supported diagnostic equipment, mechanics have the capability to easily and accurately diagnose problems in your diesel truck. These high-tech tools analyze data gathered from different sensors and systems; as a result, mechanics are able to identify problems with unparalleled accuracy. The future of diesel repair is being shaped by these advancements, which reduce time consumption while improving efficiency and ensuring that repairs are done only once, ultimately saving costs.
AI assists mechanics in remaining ahead of the curve by forecasting maintenance demands. In the future of diesel repair, AI algorithms, with the aid of historical data and patterns gathered from sensors, can anticipate things like failure points or time of servicing needed.
This innovation ensures your local mechanic is equipped not only to fix existing problems but also to intervene proactively in endangered areas. Such tools capture large amounts of data produced by sensors and systems, providing mechanics with a real-time view of the performance dynamics of your diesel truck’s engine.
For instance, AI algorithms can analyze information regarding fuel consumption and determine whether your diesel truck runs too rich or lean, showing concerns with the fuel system. If it is a problem, your mechanics will take the required steps to correct it to ensure the proper performance and life of your engine.
These suggestions promote the most effective diesel truck maintenance, increasing their performance, efficiency, reliability, and durability. By introducing AI-generated finish repairs, mechanics reduce the ‘hit and try’ approach. This makes repair processes more accurate, fixing damages and reducing downtime. Such advancements align with the future of diesel repair, paving the way for smarter and more efficient maintenance solutions.
Sensors & Connected Technologies
Along with the advent of the modern digital age, sensors and connected technologies have substantially transformed diesel truck repairs. With sensors and connected technologies, mechanics can monitor and diagnose your truck remotely.
This shift marks a pivotal development in the future of diesel repair, where mechanics will be able to monitor the performance of diesel trucks in real time and measure health indices for your diesel vehicles. Potential problems can thus be detected early on to proactively address any maintenance needs.
Mechanics capitalize on sensor technology and connections as they strive to provide unmatched services that maximize truck uptime while minimizing repair costs.
Predicting Failures Ahead in Times
Being able to predict failures in advance before they occur is a revolution as far as diesel truck repair is concerned. With the help of remote monitoring and advanced analytics, mechanics are now able to identify early signs of impending failure, which allows prompt preemptive maintenance. This advancement represents the future of diesel repair, making the industry more efficient and proactive. Predictive failure detection offers numerous benefits, including:
- Reducing downtime by preemptively fixing problems before they worsen
- Reduce expensive repairs if done early.
- Enhancing diesel truck reliability and performance
- Allows mechanics to make sure diesel truck owners use trucks that works better, and cost less in terms of repairs, driving up their overall satisfaction as customers.
The Economic Impacts of Innovative Technologies
The tech innovations in diesel repair go beyond attaining efficiency. It also cuts costs. Hence, by adopting these innovations, mechanics are able to curb costs yet deliver quality services. Below are the ways these revolutionary technologies contribute to cost reduction and increase operational efficiency in diesel repair & maintenance.
1. Increasing uptime
Through the remote diagnostic capabilities of predictive failure detection, diesel truck owners can enjoy improved uptime. Mechanics can spot potential problems early on and can work towards solving maintenance issues before they escalate. This proactive approach is shaping the future of diesel repair, ensuring that trucks remain on roads for a longer period, thereby curbing lost revenues due to repair costs.
2. Minimizing repair costs
Predictive failure detection has helped in curbing detrimental shutdowns that adversely impact operations, besides avoiding expensive repairs. The future of diesel repair increasingly emphasizes such advancements, enabling mechanics to address problems proactively. Mechanics are confronted with the problem of preventing issues from developing into complex and expensive ones.
By addressing problems at their initial stages, mechanics do not let them grow. Such proactive maintenance can be economical for truck owners who are looking to save huge repair costs and minimize the risk of emergency breakdowns and associated expenditures.
3. Improved customer satisfaction
Every company with diverse diesel trucks for transportation and logistics needs well-maintained trucks. With predictive failure detection, and correction before diesel problems become less troublesome, mechanics create a more stable solution.
The future of diesel repair lies in adopting such proactive measures, ensuring trucks remain efficient and reliable. Not only does this raise the level of customer satisfaction, but it also contributes positively to the overall reputation of the repair shop, especially when it comes to essential services like air conditioning maintenance and heating repair.
4. Increased efficacy and performance
Technological innovations for diesel repair allow mechanics to have better and efficient tools. Remote diagnostic capabilities give mechanics the ability to diagnose issues from offsite, saving invaluable time because they do not need to physically inspect your truck. By using predictive failure detection, the mechanics can arrange maintenance tasks that suit your diesel engine.
These advancements highlight the future of diesel repair, where efficiency and precision take center stage. They significantly save time because their workflow is optimized, making it efficient. This means that downtimes for repairs and service get reduced, thus giving diesel truck owners the opportunity to hit the road sooner and enjoy more productivity.
3D Printing & Virtual Reality in Diesel Repair
The diesel repair industry has been completely revolutionized by the rise of 3D printing and virtual reality. These technologies improve the mechanic’s efficiency, precision, and learning.
3D Printing of Replacement Parts
Mechanics can also duplicate diesel truck parts with the aid of 3D printing technology. This eliminates the process of waiting for the manufacturer’s spare parts. The adoption of 3D printing facilitates the fabrication process for diesel truck components, improving fuel efficiency, service life, and system run-ability.
Virtual Reality Training on Mechanics
One way or the other, VR has acted effectively to change mechanics in the likes of the diesel repair industry. VR technology enables mechanics to receive fully immersive training that are very realistic. This, in turn, gives them some real-life practice and perfects their talents within the boundaries of safety.
With the help of virtual reality, mechanics can learn how to repair complicated truck components by making mistakes on only those that were created digitally and thus causing no actual damage. They may learn how to tear down and put back together components, detect issues, and pinpoint matters that need precision. It doesn’t not only affects their technical proficiency but also proved beneficial for them by increasing confidence while operating real diesel trucks.
Also, the use of virtual reality training eliminates all costs associated with physical equipment and resources; hence both mechanics and providers benefit from the cost implications. Mechanics can use VR that is available from any location which gives them an opportunity to learn whenever they want. And do not constrain the training process by time limitations.
How New Technologies Improve Efficiency
Modern technologies, including sophisticated diagnostics tools are significantly decreasing the time of engine rebuilding and maintenance. With immediate identification of maintenance workers, auto mechanics can speed up the repair procedures for diesel truck drivers to reduce their downtime. The use of advanced technologies makes the diagnosis and repairing processes easier, focusing on efficiency boost in diesel truck repairs. These technologies streamline routine upkeep, offering diesel pickup owners assurance and guaranteeing that their vehicles operate to full capacity.
The Role of Precision in Cost Reduction
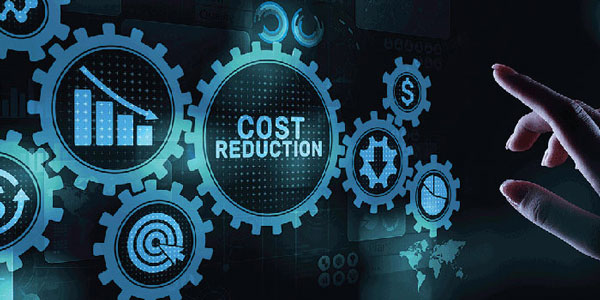
Precision is an integral part of cost reduction in diesel truck repair. Accurate engine repair, suspension alignment, and proper diagnostics promote cost-effective servicing. Correct mechanisms that diagnose and resolve the issues before more money is spent on replacement or incorrect repair help avert unnecessary spending. The future of diesel repair emphasizes the importance of precision in diagnostics and maintenance to ensure cost-effective and efficient servicing. Diesel truck maintenance has to be as precise as possible, minimizing exhaustive repair and replacement procedures in the long run.
Are Mechanics Ready for The Future of Diesel Repair?
Equipped with sophisticated diagnostic devices, virtual reality training programs, 3D printing stations, and remote monitoring systems, mechanics can guarantee a full range of services in diesel repair, including regular maintenance.
Their willingness to adapt to new technologies, such as welding and fabrication, boosts efficiency in maintenance, reduces downtime, and improves performance on diesel trucks. As the industry embraces the future of diesel repair, local repair shops stay ahead by implementing these advancements.
From truck and trailer tire repair to diesel engine repair, including roadside repairs, repair shops experienced in working with various manufacturers such as Ford provide customers with top-notch repair services.
Conclusion
The technology essentially dictates the future of diesel repair. While AI, sensors, connected technologies, 3D printing, and virtual reality are becoming more prominent in the industry, mechanics undergo adjustment to address evolving requirements.
The future of diesel repair is shaped by AI tools for engine data analysis and remote monitoring, making repairs more effective and predicting failures before they occur. Moreover, developments such as 3D printing and virtual reality training are enhancing precision and reducing costs. To enjoy the benefits of these innovations, reach out to your local motor mechanic now to get your diesel engine digitally checked
Frequently Asked Questions
How is AI shaping the future of diesel repair?
AI is revolutionizing the future of diesel repair by enabling mechanics to diagnose issues with unparalleled accuracy. Through AI-supported diagnostic tools, mechanics can analyze data from sensors to identify problems early, anticipate maintenance needs, and improve the overall performance and reliability of diesel trucks.
What role do sensors play in the future of diesel repair?
Sensors are a crucial component in the future of diesel repair, allowing mechanics to remotely monitor diesel truck performance in real time. These sensors provide valuable data to detect potential issues early, enabling proactive maintenance and reducing the likelihood of expensive repairs and downtime.
How does predictive failure detection impact the future of diesel repair?
Predictive failure detection plays a significant role in the future of diesel repair by allowing mechanics to predict issues before they occur. This proactive approach helps reduce downtime, lower repair costs, and enhance the reliability and performance of diesel trucks, ensuring a smoother operation for truck owners.
How will 3D printing and virtual reality affect the future of diesel repair?
3D printing and virtual reality are set to redefine the future of diesel repair. 3D printing allows for the creation of replacement parts on demand, reducing wait times and improving the efficiency of repairs. Virtual reality, on the other hand, provides immersive training for mechanics, improving their skills and confidence while minimizing physical resource costs.
Will the future of diesel repair lead to cost savings for truck owners?
Yes, the future of diesel repair will lead to significant cost savings for truck owners. Thanks to technologies like predictive maintenance, AI diagnostics, and remote monitoring, mechanics can address issues early, reducing costly repairs and minimizing downtime. This will ensure that diesel trucks stay on the road longer and more efficiently.